Understanding The Role of Protective Coatings in Corrosion Control
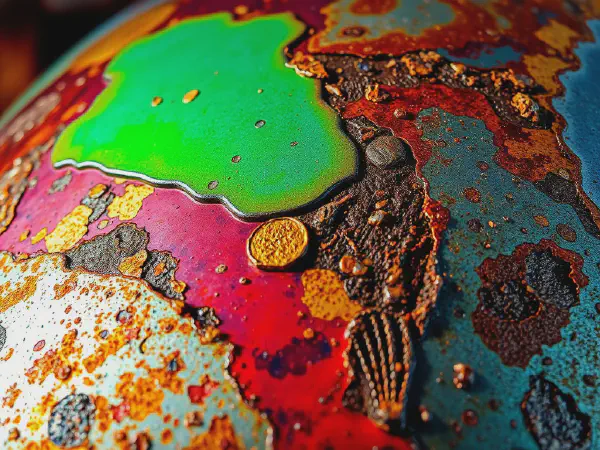
Understanding Corrosion Control: Techniques, Innovations, and Economic Impact
Corrosion control is a crucial aspect of maintaining the integrity and longevity of various structures and assets, particularly those made from metals. Corrosion, which is the gradual deterioration of materials due to environmental interactions, can lead to significant economic losses, safety hazards, and reduced operational efficiency. Effective corrosion control strategies encompass a range of techniques and remedies designed to protect materials and ensure a longer lifespan, thereby safeguarding investments and enhancing safety standards.
In today's technologically advanced environment, corrosion control has evolved beyond traditional methods. With increasing regulations and environmental considerations, the industry is leaning towards innovative solutions that are not only effective but also sustainable. From protective coatings to corrosion-resistant materials, the aim remains to mitigate the adverse effects of corrosion while minimizing environmental impact. This article provides a comprehensive overview of corrosion control, emphasizing its importance, techniques, evaluation methods, and economic implications.
The process of corrosion control is not a one-size-fits-all approach; it requires a detailed understanding of the specific material properties, environmental conditions, and potential corrosive agents. Effective strategies can involve regular monitoring, proactive maintenance, and employing advanced technologies tailored to the specific applications. Understanding these factors is vital for industries such as construction, manufacturing, and transportation, where corrosion can lead to catastrophic failures and considerable financial implications.
Moreover, advancements in materials science are paving the way for innovative corrosion control solutions. Research into novel materials and protective coatings has become a field of great interest as industries strive for sustainability and resilience against corrosion. With this in mind, the following sections further explore various types of protective coatings and the latest innovations in corrosion control, shedding light on their applications and benefits.
In conclusion, effective corrosion control is essential for preserving the integrity of assets and minimizing costs associated with corrosion damage. Employing appropriate techniques and staying abreast of innovations in the industry can significantly aid in the fight against corrosion. This not only extends the lifespan of structures and equipment but also promotes a safer and more efficient working environment.
To enhance the longevity of structures exposed to harsh environments, the application of Protective Coatings is essential.
Types of Protective Coatings in Corrosion Control
Epoxy coatings are widely used in corrosion control due to their excellent adhesion, chemical resistance, and durability. These coatings form a tough protective layer that can withstand harsh environmental conditions, making them ideal for industrial applications. The benefits of epoxy coatings include prolonged equipment life, reduced maintenance costs, and enhanced aesthetic appeal since they can be formulated in various colors and finishes to meet design requirements.
Polyurethane coatings are known for their flexibility, high gloss, and UV resistance, making them suitable for applications exposed to sunlight and moisture. They provide excellent corrosion protection while allowing the underlying substrate to expand and contract, reducing the risk of cracking or peeling. The benefits of polyurethane coatings include improved waterproofing, scratch resistance, and extended durability in outdoor environments.
Zinc-based coatings are renowned for their sacrificial properties, where the zinc corrodes preferentially to protect the underlying metal from rust. These coatings are often used in marine environments and on structures such as bridges and pipelines. The comprehensive overview of zinc-based coatings highlights their effectiveness, longevity, and cost-efficiency, making them a popular choice for corrosion protection across various industries.
Alkyd coatings are oil-based finishes that are commonly used in industrial settings thanks to their good adhesion and resistance to certain chemicals and weather conditions. These coatings are typically less expensive and can be applied easily using conventional methods. Their applications range from maintenance coatings for machinery to protective layers for metal structures, providing valuable corrosion resistance where needed.
Application Techniques for Protective Coatings
Surface preparation is critical to ensure optimal coating performance, as the adhesion between the coating and substrate significantly impacts the effectiveness of corrosion protection. Proper techniques include cleaning the surface to remove dirt, grease, and rust, as well as roughening it to enhance bonding. Different methods such as sandblasting, grinding, or chemical cleaning can be employed depending on the substrate material and condition.
When it comes to applying protective coatings, there are various techniques such as spraying and brushing, each with its own pros and cons. Spraying allows for a more even application and is ideal for large areas, while brushing is often used for detailed or smaller components. Understanding the nuances of each method can help in selecting the most suitable application technique based on the project's specific requirements.
The curing process of protective coatings is essential for achieving maximum durability and performance. Different types of coatings require specific curing conditions, which may involve heat or controlled humidity. Awareness of the correct curing processes ensures that the coatings achieve their full potential in terms of hardness, adhesion, and resistance to environmental factors.
Common mistakes in coating application can lead to significant failures, emphasizing the importance of following best practices. These include insufficient surface preparation, improper mixing of components, and neglecting environmental conditions during application. Training staff and implementing quality checks can greatly reduce these errors and enhance the overall integrity of the corrosion control solution.
Performance Evaluation of Protective Coatings
Testing methods for coating durability are fundamental to evaluate performance and longevity. Techniques such as adhesion tests, impact resistance tests, and salt spray tests are commonly used to determine how well the coatings withstand various stresses and corrosive environments. Regular testing helps in identifying the performance levels of protective coatings and in making informed decisions about their application in different contexts.
The impact of environmental conditions on coating performance cannot be overstated. Factors such as humidity, temperature, and exposure to harsh chemicals influence the effectiveness of protective coatings significantly. Monitoring environmental conditions and performing durability assessments ensure that coatings can be tailored to specific scenarios, optimizing corrosion control efforts.
Lifecycle analysis of coatings for corrosion protection is vital for understanding the total cost of ownership and effectiveness over time. Evaluating factors such as application costs, maintenance needs, and replacement frequency contributes to a comprehensive approach to corrosion control. This analysis helps industries to make economically sound decisions regarding their coating investments.
Standards and regulations in coating evaluation establish benchmarks for quality and performance. Compliance with industry standards, such as ISO and ASTM, ensures that coatings meet safety, reliability, and environmental requirements. Adhering to these guidelines not only enhances performance but also builds trust and confidence in corrosion control solutions.
Innovations in Protective Coatings
Nanotechnology in coatings represents a groundbreaking advancement in corrosion control. The incorporation of nanoparticles into coating formulations enhances their properties, providing improved barrier resistance, self-cleaning capabilities, and even anti-corrosive effects. These innovations open new avenues for extending the lifespan of materials while reducing maintenance costs and environmental impact.
Smart coatings are an exciting development in corrosion control that offer real-time monitoring capabilities. These coatings can change color or provide alerts when corrosion is detected, allowing for proactive maintenance. The features and benefits of smart coatings can drastically improve maintenance strategies, preventing costly failures and extending the life cycle of assets.
Environmentally friendly coatings are gaining traction as industries move towards sustainable solutions. These coatings often employ bio-based materials, reduced volatile organic compounds (VOCs), and recyclable components, adhering to stringent environmental standards. The trends and outlook for such coatings indicate a growing demand for sustainable practices that do not compromise performance or safety.
Self-healing coatings are a revolutionary innovation that can significantly enhance longevity. These advanced coatings contain microcapsules filled with healing agents that, when damage occurs, release the agent to repair scratches or abrasions. As a result, self-healing coatings maintain integrity and effectiveness over time, representing a major leap in corrosion control technology.
Cost-Benefit Analysis of Protective Coatings
Conducting a thorough cost-benefit analysis of protective coatings reveals the balance between initial investment and long-term savings. While the upfront costs of high-quality coatings may be substantial, the reductions in maintenance costs and the risks associated with corrosion failures can lead to significant savings over the asset's lifespan. Assessing these factors is crucial for stakeholders looking to maximize their investment.
Comparing different coating materials is essential in understanding the financial implications of corrosion control. By analyzing the performance, durability, and application costs of various materials, decision-makers can select the most economically viable option that meets their specific needs without sacrificing quality or performance.
The economic impact of corrosion on industries is staggering, with estimates indicating that corrosion costs billions of dollars annually. Industries like oil and gas, transportation, and infrastructure significantly bear the burden of corrosion-related expenses, highlighting the importance of investing in effective corrosion control strategies.
Finally, financial justification for coating applications requires a robust understanding of the long-term benefits gained from effective corrosion control measures. By showcasing evidence of cost savings, performance improvements, and compliance with regulations, businesses can secure the necessary funding to implement advanced protective coatings that will ultimately protect their investments.