Understanding Protective Coatings for Effective Corrosion Control
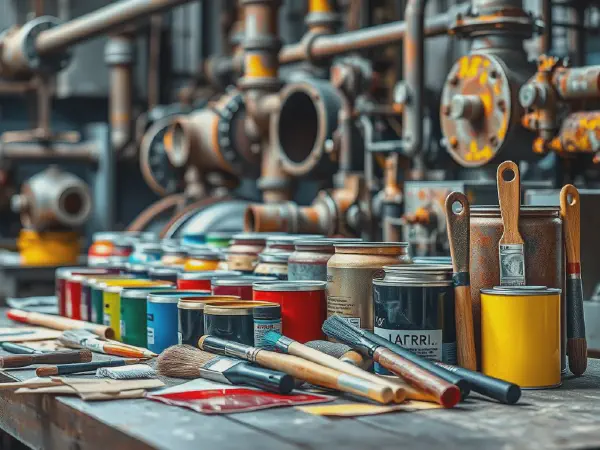
The Role of Protective Coatings in Corrosion Control
Corrosion is a natural process that deteriorates metals and other materials, leading to significant economic losses and safety hazards. Protective coatings play a vital role in corrosion control by creating a barrier that prevents environmental factors from reaching the substrate. This article explores the various aspects of protective coatings in corrosion control, including their types, applications, mechanisms of action, testing methods, and future trends.
The Role of Protective Coatings in Corrosion Control is paramount, as it directly influences the lifespan and durability of structures and equipment across various industries. Protective coatings mitigate rust formation and the degradation of surfaces exposed to challenging environments, ultimately reducing maintenance costs and enhancing operational safety. These coatings not only serve as a physical barrier but may also include properties like chemical resistance, elasticity, and UV protection, depending on the specific requirements of the application.
In many sectors, such as construction, automotive, and manufacturing, the use of protective coatings has become standardized practice due to their effectiveness in prolonging the life of assets. As industry standards evolve and environmental regulations tighten, the need for innovative and high-performance coatings that address specific corrosion challenges is growing. This article will delve into the types of protective coatings, their applications, the underlying corrosion mechanisms, the testing and evaluation processes for coatings, and the emerging trends that promise enhancements in corrosion prevention.
From industrial equipment and marine vessels to architectural structures and automobiles, protective coatings are essential in combating corrosion. This article aims to provide a comprehensive understanding of how protective coatings function, the variety of options available, and the future landscape of corrosion control technologies. By understanding the role of protective coatings in corrosion control, manufacturers and asset managers can make informed decisions that enhance equipment longevity and safety.
In light of increasing pressures for sustainability and performance, investing in high-quality protective coatings is a strategic decision that significantly impacts operational efficiency and cost-effectiveness. Therefore, understanding and applying the principles of protective coatings in corrosion control is crucial for any organization seeking to maintain reliable and safe operations.
Types of Protective Coatings
There are several types of protective coatings that serve specific corrosion control functions, primarily categorized into organic and inorganic coatings. Organic coatings, such as paints and polyurethanes, provide a flexible and aesthetically pleasing option for various applications. These coatings can be formulated with specific additives to enhance their performance, such as UV resistance and abrasion resistance, making them suitable for both interior and exterior uses.
Inorganic coatings, including zinc and epoxy, offer superior corrosion resistance properties. Zinc coatings employ the cathodic protection mechanism, where the zinc acts as a sacrificial anode, preventing corrosion of the underlying metal. Epoxy coatings form a resilient bond and are highly impermeable, shielding substrates from moisture and corrosive chemicals. Both these categories of coatings are essential in heavy-duty industrial environments.
Thermal sprayed coatings involve the application of melted or heated materials that are sprayed onto a substrate. This method allows for thick coatings and is commonly used for components exposed to extreme conditions. The result is a robust layer that can withstand harsh environments and extend the life of industrial machinery.
Implementing effective Protective Coatings is crucial for extending the lifespan of infrastructure in challenging environments.
Nano-coatings represent a recent innovation in protective coatings, offering enhanced protection through microscopic structures that provide superior barriers against corrosion. These coatings can be engineered for specific properties like hydrophobicity, improving water resistance, and decreasing the adhesion of contaminants, making them ideal for a wide range of applications, making them a fascinating area of development in corrosion prevention.
Applications of Protective Coatings
Protective coatings find widespread applications across various industries. In industrial equipment, coatings are critical for enhancing corrosion resistance and maintaining equipment reliability in sectors such as oil and gas, power generation, and manufacturing. These coatings can significantly reduce downtime and maintenance costs by preventing premature failure caused by corrosive elements.
In marine applications, protective coatings are vital for the longevity of ships and offshore structures. Choices of coatings take into consideration factors such as water salinity, biological growth, and exposure to harsh weather. Marine coatings, particularly antifouling types, are engineered to prevent the growth of organisms on vessel hulls, which can lead to increased fuel consumption and compromised structural integrity.
Architecturally, protective coatings are employed to protect buildings and infrastructure from corrosion, contributing to both aesthetic appeal and structural integrity. Coatings are designed specifically for exterior surfaces, ensuring long-term durability against weather elements. They can also contribute to energy savings by reflecting UV radiation or by exhibiting thermal insulation properties.
In the automotive industry, coatings play a significant role in preventing rust, enhancing vehicle aesthetics, and protecting surfaces from scratches and environmental damage. Innovations in coating technologies include self-healing properties and improved adhesion, which ensure that vehicles remain protected over time, a critical aspect for manufacturers aiming for improved sustainability and customer satisfaction.
Corrosion Mechanisms
Understanding corrosion mechanisms is vital for developing effective protective coatings. Electrochemical corrosion is one of the main types, occurring when metals are in contact with an electrolyte, and an electric current flows. The interaction can lead to metal loss, which is why protective coatings are necessary to create a barrier to these corrosive elements.
Environmental factors influencing corrosion include temperature, humidity, and exposure to industrial pollutants. Each factor can accelerate the rate of corrosion, making it crucial to consider these elements when selecting protective coatings. For instance, in humid environments, coatings with moisture barrier properties are essential to mitigate corrosion risks.
The role of pH and salinity in corrosion processes is also significant. High salinity levels can exacerbate corrosion rates, particularly in coastal areas where concrete structures are prevalent. Coatings engineered with specific chemistries can help counteract the adverse effects of pH variations, ensuring better corrosion resistance in diverse environments.
Galvanic corrosion occurs when two different metals are in electrical contact in a corrosive environment. Protective coatings can prevent this by insulating the metals’ surfaces and reducing the risk of such electrochemical reactions. Understanding these mechanisms helps in the development of coatings tailored for specific applications and environments.
Testing and Evaluation of Coatings
Adhesion testing methods are crucial for assessing the integrity of protective coatings. Techniques such as pull-off tests and cross-cut adhesion tests reveal the strength of the bond between the coating and the substrate. A strong adhesion ensures that the protective function remains intact over time, which is essential for effective corrosion control.
Corrosion resistance testing methods, including salt spray (fog) tests and cyclic corrosion tests, evaluate how well coatings can withstand corrosive environments. These standardized tests simulate real-world conditions to assess performance and durability, providing valuable data before coatings are applied to critical assets.
Long-term performance evaluation is vital for understanding how coatings will perform over time. This insight can be gathered through long-term exposure studies and assessing the physical and chemical properties of coatings after extended periods under operational conditions. Such evaluations help in ensuring the reliability and effectiveness of protective coatings.
Field testing versus laboratory testing plays a significant role in coatings assessment. While laboratory tests offer controlled conditions and repeatability, field tests provide real-world data about how coatings withstand actual environmental conditions and stresses. A combination of both testing strategies is often employed to ensure thorough evaluation and validation of coating performance.
Future Trends in Protective Coatings
The demand for bio-based and eco-friendly coatings is growing as industries shift towards more sustainable practices. These coatings minimize environmental impact and health concerns associated with traditional solvent-based options, addressing the need for greener alternatives without compromising performance.
Advances in self-healing coatings represent another innovative trend in protective coatings. These coatings can autonomously repair damage caused by scratches or wear, extending their functional lifespan and reducing the need for maintenance or reapplication, which is a significant advancement in corrosion control methods.
Digital monitoring of coating integrity is emerging as a valuable tool in corrosion management. Technologies such as sensors and IoT devices can be integrated to provide real-time data on coating health and environmental conditions. This proactive approach enhances the monitoring and maintenance of protective coatings, ensuring timely interventions and minimizing potential damage.
Lastly, the continued integration of nanotechnology into protective coatings offers new possibilities for innovation. These coatings can exhibit unique properties such as extreme hardness, enhanced durability, and improved resistance to environmental degradation. As research advances, these innovations will play a crucial role in developing the next generation of protective coatings tailored for optimal corrosion control.