Top Rust Prevention Tips You Can't Afford to Ignore
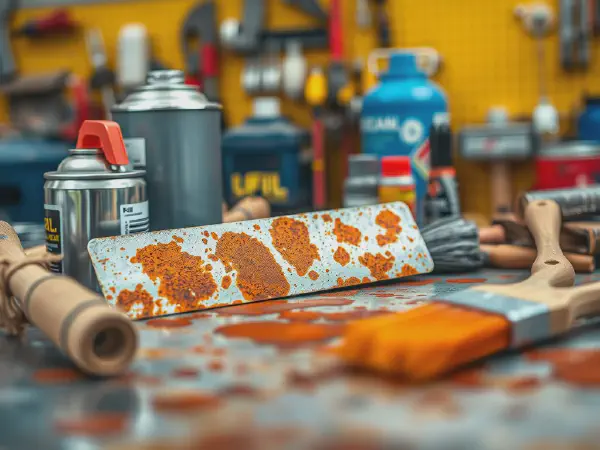
Rust Prevention: Strategies for Protecting Metal Assets
Rust prevention is a critical aspect of maintaining the durability and lifespan of metal structures and equipment. Rust, which is the result of oxidation, can significantly weaken metal components and lead to expensive repairs or replacements. Therefore, implementing effective rust prevention strategies is essential for both individuals and businesses to protect their assets from corrosion.
The process of rust prevention involves various methods and techniques, from chemical treatments to protective coatings, each designed to hinder the oxidation process. A proactive approach can save time and resources, ensuring that metal surfaces remain intact and reliable. Understanding the appropriate methods and their application is key to effective rust prevention.
Another critical dimension of rust prevention encompasses regular maintenance practices. Routine inspections and cleaning can go a long way in detecting early signs of rust and addressing any potential vulnerabilities. By incorporating maintenance into the overall strategy, one can effectively minimize rust formation and promote the longevity of metal products.
Environmental factors also play a significant role in the rate of rust formation. High humidity, temperature fluctuations, and exposure to corrosive substances can all accelerate oxidation processes. Recognizing these factors allows for targeted rust prevention measures that can mitigate risk and protect assets.
Implementing effective strategies for Rust prevention is essential to prolonging the lifespan of metal structures.
Finally, innovative technologies in rust prevention are paving the way for more efficient and durable solutions. From advanced chemical treatments to nanotechnology, these emerging methods offer promising prospects for enhancing rust resistance in various applications, heralding a new era in metal preservation.
Chemical Treatments for Rust Prevention
Rust-inhibiting chemicals play a vital role in rust prevention. These substances can be applied to metal surfaces to form a protective layer that reduces oxidation. Common chemicals include rust converters, which transform existing rust into a stable substance, and rust inhibitors that prevent new rust from forming by providing a barrier against moisture and oxygen.
To apply rust prevention coatings effectively, the surface must first be cleaned to remove any dirt, grease, or existing rust. After cleaning, the rust-inhibiting chemical can be applied using brushes, rollers, or spray equipment, depending on the product's specifications. Proper application ensures even coverage and maximum protection against rust.
A comparative analysis of rust prevention chemicals reveals several options with varying effectiveness and application methods. For instance, zinc-based primers are known for their galvanic protection, while oil-based coatings provide a robust water-resistant layer. Each type of rust prevention chemical comes with advantages and considerations that must be evaluated based on the specific application and environmental conditions.
Barriers and Coatings to Prevent Rust
Barriers for rust prevention can be categorized into several types, including paints, powder coatings, and galvanizing. Paints are versatile and can offer varying levels of protection depending on their formulation, while powder coatings are applied electrostatically and cure to form a hard finish resistant to chipping, scratching, and fading. Galvanizing involves coating steel with a layer of zinc, providing cathodic protection.
The benefits of using protective coatings extend beyond rust prevention. These coatings can enhance aesthetic appeal, improve surface hardness, and provide additional resistance to impact and chemical exposure. They serve dual roles as both protective barriers and finishes that can improve the overall performance of metal products.
Application methods for rust prevention barriers vary according to the type of coating being used. Ceramic coatings may require professional application due to their complexity, while paints and powders can often be applied by the end user with appropriate tools and safety precautions. Ensuring the correct application method is crucial for maximizing the effectiveness of the preventative measures in place.
Maintenance Practices for Rust-Free Surfaces
Routine inspections are an essential practice for effective rust prevention. Regularly checking metal surfaces for any signs of rust, paint blisters, or paint loss enables early detection and intervention, which can prevent more extensive corrosion and damage.
Cleaning techniques to prevent rust typically involve removing contaminants that can trap moisture and promote oxidation. Using a mixture of water and mild detergent to regularly clean metal surfaces can help deter rust. For more severe cases, abrasive cleaning techniques like sandblasting may be necessary to remove rust and prepare the surface for re-coating.
Best practices for maintaining metal surfaces include keeping them dry, storing them in a climate-controlled area, and avoiding exposure to corrosive substances. Additionally, applying touch-up paint or re-coating damaged areas promptly helps maintain a barrier against rust and extends the life of metal assets.
Environmental Factors Affecting Rust
Humidity significantly impacts rust formation, as moisture in the air can accelerate the oxidation of metal. Environments with high humidity levels, especially coastal areas, pose a greater risk for rust, making it vital to implement robust rust prevention measures in such locations.
Temperature influences rusting by affecting the rate of chemical reactions. Warmer temperatures can speed up the oxidation process, while colder conditions may slow it down but not eliminate the risk entirely. Understanding the temperature extremes to which metal is exposed can inform the choice of protective measures.
Identifying high-risk areas for rust involves assessing environmental exposures as well as the specific use cases for metal assets. Areas that experience frequent wetting, such as those exposed to rain or industrial processes that use water, should be prioritized for intensive rust prevention measures to safeguard against corrosion.
Innovative Technologies in Rust Prevention
New advancements in rust prevention methods include the development of more effective rust inhibitors, self-healing coatings, and advanced corrosion-resistant materials. These technologies aim to provide longer-lasting protection and require less frequent maintenance, helping to streamline the process of rust prevention.
Nanotechnology is playing an increasingly important role in rust inhibition. By manipulating materials at a molecular level, researchers are creating coatings that offer superior protective properties. These nano-coatings can be remarkably thin while providing enhanced resistance to rust formation, offering innovative solutions for modern industry.
Modern rust prevention technologies are designed for durability and efficiency, often outlasting traditional methods. These advancements save costs over time by reducing the frequency and intensity of maintenance needed, ensuring that metal assets remain protected for extended periods without significant intervention.