Exploring Anti-Corrosion Paints: Uses and Benefits
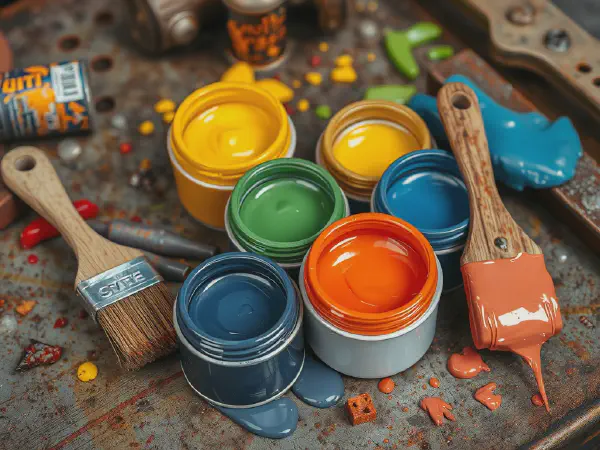
Understanding Anti-Corrosion Paints and Their Importance
Anti-Corrosion Paints are specialized coatings designed to protect metal surfaces from rust and degradation caused by environmental factors. These paints are essential in a wide range of industries and applications, providing a barrier that prevents moisture, salt, and chemicals from corroding the underlying material. The use of Anti-Corrosion Paints enhances the durability and longevity of structures and objects exposed to harsh conditions.
The effectiveness of Anti-Corrosion Paints is derived from their composition, which often includes rust inhibitors and other ingredients that form a protective layer. Industries utilizing these paints span from maritime to automotive, construction to manufacturing, showcasing their versatility and critical role in asset protection. Understanding the different types of Anti-Corrosion Paints available can aid in selecting the most appropriate solution for various applications.
Using Anti-Corrosion Paints can significantly extend the lifespan of metal surfaces in harsh environments.
Anti-Corrosion Paints come in various formulations, each tailored to specific environmental conditions and types of surfaces. Some common formulations include epoxy-based coatings, polyurethane coatings, and zinc-rich paints. With the growing emphasis on environmental sustainability, water-based anti-corrosion solutions are also gaining popularity due to their lower VOC emissions. Proper application and compliance with regulatory standards are essential to maximize the performance of these paints.
As corrosion continues to pose significant challenges across industries, the development and advancement of Anti-Corrosion Paint technologies are of paramount importance. The integration of new additives and innovative application methods enhances both performance and eco-friendliness. This article delves deeper into the specific types, applications, benefits, techniques, and regulatory standards of Anti-Corrosion Paints, providing a comprehensive understanding for professionals and end-users alike.
Ultimately, investing in Anti-Corrosion Paints is investing in the longevity and reliability of structures and equipment. With proper selection and application, these paints help mitigate corrosion risks, reduce maintenance costs, and enhance overall safety.
Types of Anti-Corrosion Paints
Epoxy-based anti-corrosion paints are highly regarded for their exceptional adhesion and chemical resistance. They are ideal for use on metal surfaces that are exposed to harsh environments, as they provide a robust barrier against moisture and chemicals. These paints typically consist of a base and a hardener that, when mixed, cure to form a tough protective coating.
Polyurethane anti-corrosion coatings are known for their flexibility and UV resistance, making them suitable for both indoor and outdoor applications. They offer excellent abrasion resistance and can be applied over previously painted surfaces. Polyurethane coatings are also available in a range of finishes, adding aesthetic value to surfaces while ensuring protection.
Zinc-rich anti-corrosion paints contain a high percentage of zinc dust, which provides sacrificial protection to the underlying metal. When applied, the zinc oxidizes and corrodes before the metal does, effectively prolonging its life. These paints are commonly used in industrial settings, particularly for steel structures, where they are applied as a primer.
Water-based anti-corrosion solutions are increasingly popular due to their lower environmental impact compared to solvent-based products. They offer ease of application and clean-up while providing effective corrosion protection. Water-based paints are suitable for a variety of substrates and are often used in areas where VOC emissions need to be minimized.
Thermal spray coatings for corrosion resistance involve the application of metallic coatings (such as zinc or aluminum) onto a surface through a spray process. This method provides a robust protective layer that can withstand severe environmental conditions, making it ideal for marine applications and industries that demand high-performance coatings.
Applications of Anti-Corrosion Paints
Anti-Corrosion Paints play an essential role in marine environments, where saltwater exposure can lead to rapid corrosion of ships and offshore structures. These paints are formulated to withstand harsh marine conditions, ensuring the longevity of vessels and marine equipment.
In industrial settings, equipment often undergoes wear and tear due to exposure to chemicals and varying temperatures. Anti-Corrosion Paints protect machinery, pipelines, and storage tanks, preventing costly repairs and downtime resulting from corrosion-related failures.
Infrastructure such as bridges and roads is critical to public safety and requires regular maintenance. Anti-Corrosion Paints help protect structural components from corrosion, extending their lifespan and ensuring safe usage for the public.
In the automotive and transportation sectors, Anti-Corrosion Paints are applied to vehicles and parts to prevent rust, especially in regions where vehicles are exposed to salt on roads. These coatings help maintain the appearance and structural integrity of vehicles over time.
The oil and gas industry heavily relies on Anti-Corrosion Paints to protect pipelines, rigs, and storage facilities. Given the harsh conditions these facilities operate under, effective coatings are vital for preventing leaks and ensuring safe operations.
Benefits of Using Anti-Corrosion Paints
One of the primary benefits of using Anti-Corrosion Paints is the extended lifespan they provide to surfaces. By preventing corrosion, these paints help maintain the structural integrity of metal components, reducing the need for frequent replacements and repairs.
Cost-effectiveness in maintenance is another significant advantage. Regular application of Anti-Corrosion Paints can lead to substantial savings over time by minimizing the frequency of maintenance and the associated costs of repairs or replacements due to corrosion damage.
Using Anti-Corrosion Paints also enhances safety and reliability. In critical sectors such as transportation and construction, maintaining equipment and structural assets free of corrosion hazards ensures safety for workers and the public.
Environmental protection and sustainability are increasingly important considerations in today’s industry. Many Anti-Corrosion Paints are formulated with eco-friendly ingredients and low VOC emissions, contributing to a healthier environment.
Aesthetic enhancements are also a benefit of Anti-Corrosion Paints. With a variety of colors and finishes available, these coatings can improve the appearance of industrial applications while maintaining their protective performance.
Application Techniques for Anti-Corrosion Paints
Surface preparation is a critical first step in applying Anti-Corrosion Paints. Proper cleaning, sanding, and priming of surfaces ensure optimal adhesion of the paint, which is vital for effective corrosion protection.
Spray application techniques are often preferred for large-scale projects, as they provide a uniform coat and reduce application time. However, proper equipment and skilled operators are necessary to achieve the desired results with spray techniques.
Brush and roll application processes are recommended for smaller areas or detailed work. These methods allow for thorough coverage and are ideal for touch-ups or applications in tight spaces.
Curing and drying times can vary depending on the type of Anti-Corrosion Paint used. Understanding these times is essential for ensuring that the coating fully adheres and achieves its protective properties before exposure to environmental factors.
Common mistakes to avoid during the application of Anti-Corrosion Paints include neglecting surface preparation and applying the paint under unsuitable weather conditions, which can affect adhesion and performance.
Regulatory Standards for Anti-Corrosion Paints
Environmental regulations have a significant impact on the formulation and application of Anti-Corrosion Paints. Compliance with regulations ensures that products do not harm the environment or public health, leading to the development of eco-friendlier options.
ISO standards for corrosion protection set benchmarks for quality and performance. Adhering to these standards ensures that Anti-Corrosion Paints meet specific efficacy and safety requirements across various industries.
Industry-specific compliance requirements often dictate the types of coatings that can be used in sensitive environments, such as the food and beverage industry or healthcare facilities, where contamination risks must be minimized.
Certification processes for anti-corrosion products provide assurance of quality and reliability. Recognized certifications can enhance marketability and customer trust in the performance of Anti-Corrosion Paints.
Choosing compliant products for projects is crucial to ensure that they meet necessary regulatory standards and provide effective corrosion protection. Consulting with experts and reviewing product certifications can aid in making informed decisions.